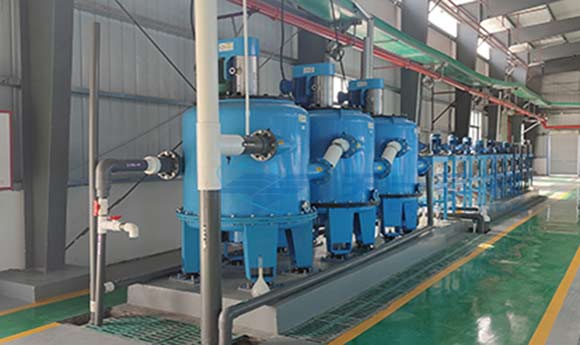
Rare earth elements play an indispensable role in the high-tech field due to their unique physical and chemical properties and are known as "industrial vitamins". However, the ion radius of lanthanide elements differs by less than 0.01Å and their chemical properties are highly similar, which means that traditional solvent extraction methods require hundreds of mixer settlers to be connected in series to achieve effective separation. This multi-stage series method is not only time-consuming and energy-intensive, but also has huge equipment investment and operating costs, which makes it difficult to meet the needs of modern industry. In recent years, centrifugal extraction technology has gradually become the mainstream solution in the field of rare earth separation due to its high efficiency and environmental protection.
The separation of rare earth minerals is extremely difficult. Taking mixed rare earth ores as an example, lanthanide elements form a complex coordination system with symbiotic elements such as yttrium and scandium. Conventional extraction equipment needs to go through more than 300 theoretical stages to achieve effective separation. This multi-stage series connection makes it difficult to achieve both separation purity and efficiency. The centrifugal extractor can be used. The working principle of centrifugal extraction technology is to use a motor to drive the drum to rotate at high speed. Two liquids with different densities and immiscible with each other complete the mixing and mass transfer under the shear force generated by the rotation of the drum or blades, and then quickly separate under the centrifugal force generated by the high-speed rotation of the drum, overcoming many disadvantages of traditional methods.
Taking Sichuan fluorocarbon cerium ore as an example, the typical process flow of treating rare earth ore pulp using centrifugal extraction technology is as follows:
- Countercurrent extraction: The ore pulp containing rare earth is countercurrently contacted with the extractant (such as P507), and the rare earth is preferentially complexed with the extractant and enters the organic phase.
- Washing and purification: The organic phase loaded with rare earth is washed with dilute acid to remove the trace impurities entrained and further improve the purity of rare earth.
- Stripping: The rare earth in the organic phase is stripped with an acidic solution to obtain a high-purity rare earth enriched solution.
Process innovation and practical application cases show that when centrifugal extractor is used to treat Sichuan fluorocarbon cerium ore, the extraction rate of lanthanum can reach 99.2%, and the separation coefficient of coexisting impurity ions is increased by 3 orders of magnitude compared with the traditional process. This breakthrough performance improvement is due to the precise control of the interphase behavior by the centrifugal field: under the action of Taylor vortex, the contact surface of the two phases shows periodic fluctuations, which not only strengthens micro-mixing but also promotes interphase renewal, forming a dynamically balanced mass transfer channel.
The application of the centrifugal extractor with all-corrosion-resistant reinforced materials in rare earth extraction and separation not only solves the problems of low efficiency and serious environmental pollution of traditional separation methods, but also provides strong technical support for the green transformation of the rare earth industry.
The following are its main application effects:
- High recovery rate: The rare earth recovery rate reaches 98.8%, which is much higher than the traditional process.
- Energy saving and environmental protection: The solvent recycling rate is as high as 90%, and the wastewater discharge is reduced by 60%, which greatly reduces environmental pollution.
- Significant economic benefits: The unit product power consumption is reduced by 38%, the floor area is reduced by 70%, and the production cost is greatly reduced.
- Wide range of applications: It can be applied to new energy and new materials, hydrometallurgy, environmental governance and other fields, and is widely adapted to liquid materials of different densities and viscosities.
The application of centrifugal extractors made of fully anti-corrosion reinforced materials in rare earth extraction and separation not only achieves efficient separation of rare earth elements, but also promotes the development of the rare earth industry in a green and efficient direction. Through efficient mass transfer processes, rapid separation capabilities and intelligent control methods, centrifugal extraction technology has greatly improved the recovery rate and product quality of rare earths, and reduced production costs and environmental impacts.
Email: sales@tieiextraction.com
Whatsapp: +86 19069612820