In recent years, with the development of lithium ion battery cathode materials from single lithium cobalate or lithium manganate to lithium nickel cobalt manganate ternary with precise coordination and strict impurity concentration control, the purity of manganese sulfate is required to be very high, especially the content of harmful impurities such as potassium, sodium, calcium and magnesium must be controlled.
The methods for removing calcium and magnesium from manganese sulfate mainly include crystallization, electrolysis, chemical precipitation and extraction.
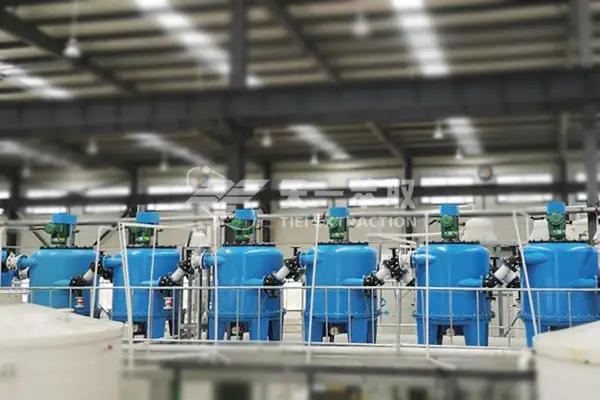
In order to overcome the shortcomings of the existing technology, Tiei Extraction recommended the centrifugal extraction system of manganese sulfate, which has the advantages of short process, high efficiency, low energy consumption, which can be prepared battery grade high-purity manganese sulfate.
The core of the system is the centrifugal extraction section, washing section and stripping section. The main equipment is CWL-M series centrifugal extractor, which has low energy consumption and high extraction efficiency. It is made of corrosion resistant PVDF, widely used in the extraction of rare earth, nickel, cobalt, manganese, lithium and copper in hydrometallurgy.
Case show:
Manganese sulfate extraction process designed by Tiei Extraction for a factory in Shanghai: 4-stage extraction section+8-stage washing+6-stage stripping.
The solvent extractant is composed of cyanex 272 and sulfonated kerosene as diluent. Mg2+and ca2+in the manganese sulfate solution were reduced to 3.12mg/l and 1.18mg/l respectively after being treated by the centrifugal extraction device, after extraction, the final products can be reaching the battery grade high-purity manganese sulfate index.