As the active component of the catalyst, nickel is mainly used in the hydrogenation process, such as the hydrofining of petroleum fractions, oil and fat hydrogenation, etc. The nickel content is higher to 6%~20% in the spent nickel catalyst generated in the hydrogenation process, which is much higher than the nickel content in the lean ore. The solid waste represented by the spent nickel catalyst is called the "secondary resource". Nickel exists in two forms of Ni and Nio in spent nickel catalyst.
Generally speaking, nickel is first oxidized to nickel oxide under high temperature for nickel recovery, and then iron is removed through acid leaching and oxidation. The filtered nickel solution is extracted to extract nickel in the form of nickel sulfate. As the spent nickel catalyst contains more impurities zinc, the chemical properties of zinc and nickel are very similar, and it is difficult to separate them from each other. Zinc has an impact on nickel extraction, resulting in a decrease in nickel extraction rate and purity.
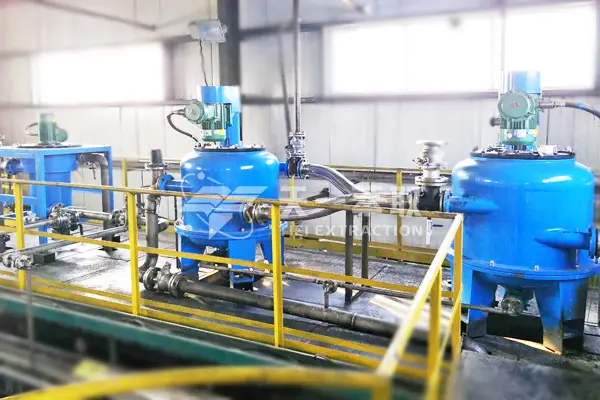
The method of recovering nickel from waste catalyst introduced by Zhengzhou Tiei Extraction is innovative in the following two aspects:
1. Using mixed reagents, by changing the selectivity of solvent extractant, can improved the Nickel extraction recovery rate;
2. Adopted the environmental CWL-M centrifugal extraction technology, is a green extraction process based on the principle of cation exchange and complexation extraction in metal extraction and CWL-M extraction equipment application.
Roasting desulfurization Process:
The spent nickel catalyst is oxidized and calcined in the rotary kiln, and the sulfur enters the flue gas in the form of hydrogen sulfide or sulfur dioxide, and the sulfur impurities are neutralized by lime;
Leaching Process:
The desulfurized materials are broken, and the materials with particle size less than 100 mesh are leached by adding 92.5wt% sulfuric acid;
Adjust PH Process:
After adding hydrogen peroxide to the leachate for oxidation for 30min, add powdered industrial soda ash to neutralize it until the solution ph=10, and filter it to remove iron;
Extraction Process
CWL-M series centrifugal extractor is used as the core extraction equipment.
The ratio of nickel sulfate metal solution and solvent extractant P204, diluent kerosene and industrial white oil is 17~19:70~75:8~12. They enter CWL-M series centrifugal extractor from their respective feed inlet 1 for extraction stripping to obtain organic phase and aqueous phase containing nickel sulfate. The organic phase returns to the extraction process for secondary extraction.
CWL-M series centrifugal extractor manufactured by Zhengzhou Tiei Extraction, has following characteristics: ① high metal extraction rate; ② Simple process flow and convenient operation; ③ The obtained stripping solution has stable quality and can meet different production requirements; ④ The residual amount of aqueous solvent after treatment is less, which can reduce the treatment pressure of subsequent sections; ⑤ The extraction equipment occupies less area and has large processing flexibility.
Evaporative crystallization Process:
The aqueous phase containing nickel sulfate was evaporated and crystallized at 105 ℃ for 4h to produce refined nickel sulfate.
In this process, the extraction rate of nickel can be increased to 95%, and the purity of nickel can reach the grade of refined nickel sulfate.