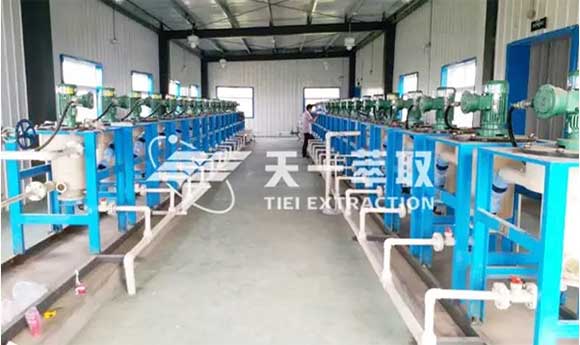
Nitrotoluene is an important organic intermediate, widely used in explosives, medicine, dyes and other fields. In industrial production, its synthesis and refining process involves key separation and neutralization dephenolization steps.
Centrifugal Extractor Process Principle
The toluene nitration reaction adopts a continuous nitration process in which a ring nitrator and a nitrification pot are connected in series. Mixed nitric acid and sulfuric acid are used as mixed acid, and enter the system in proportion with toluene and circulating acid to generate mixed nitrotoluene. After the reaction, the finished product is obtained through separation, neutralization, dephenolization, water washing and other processes.
Separation is based on the difference in specific gravity. The oil phase (nitrotoluene) and the acid phase (circulating acid) are separated by a three-stage oil-water separator; neutralization and dephenolization use dilute alkali solution to remove residual acid and phenolic by-products. However, in this process, problems such as precipitation of sodium phenolate, equipment blockage, and incomplete phase separation often occur, affecting product quality and efficiency.
Process Optimization Solution
•Improve temperature control: improve reaction temperature accuracy and increase yield.
•Enhance stirring effect: optimize agitator structure and speed to improve mass transfer efficiency.
•Adjust alkali solution concentration: find the best ratio to enhance dephenolization effect.
•Upgrade separation equipment: introduce high-efficiency centrifugal extractor to replace traditional layering device.
•Optimize process flow: simplify operation steps and improve automation level.
Through preliminary experimental verification, the control of alkali solution concentration and temperature has achieved initial results, but the improvement is limited. Finally, it was decided to focus on in-depth research on centrifugal extraction equipment and process optimization.
Experimental Verification and Result Analysis
- Separation experiment: CWL-M series centrifugal extractor was used to separate the organic phase and acid phase in the nitrification liquid. The experiment showed that in the feed flow range of 200~600mL/min, the two phases were well separated when the weir plate size was 30.5mm, there was no obvious entrainment in the light phase, and only a small amount of oil on the surface of the heavy phase. After changing to a 29.5mm weir plate, the oil droplets were reduced and the system operated stably.
- Alkali washing experiment: The organic phase after nitration was subjected to alkaline washing test with sodium hydroxide solution of different concentrations through CWL-M series centrifugal extractor. The results showed that when the ratio of alkali solution to organic phase was 2:1 and the total flux was 300mL/min, the content of sodium phenolate was significantly reduced. However, sodium phenolate is easy to precipitate at low temperature, causing equipment blockage. After the temperature was raised to 50°C, no crystallization was observed, the two phases were clearly separated, and the system operated smoothly.
- Washing experiment: The organic phase after alkali washing was washed with deionized water. Increasing the temperature can effectively improve the phase separation effect. There is no obvious entrainment between the two phases, the water phase is clear, and the color of the organic phase is normal. The feed rate increased from 250mL/min to 750mL/min and still maintained good separation performance.
Conclusion and Recommendations
Through a series of experimental verifications, the following conclusions were drawn:
- Under reasonable working conditions, the CWL-M series centrifugal extractor can effectively separate the organic phase from the acid phase, alkaline washing liquid, and water washing liquid in the nitrification liquid.
- Temperature control is crucial to the alkaline washing effect and needs to be maintained above 40°C to prevent the precipitation of sodium phenolate.
- The weir plate size selection needs to be flexibly adjusted according to the density changes of the two phases, but it is difficult to replace it in real time during continuous production, which limits its adaptability.
- The CWL-M series centrifugal extraction technology is suitable for production environments with stable working conditions and continuous feeding. For operating conditions with large fluctuations, it is recommended to retain the original stratification equipment or combine the advantages of both to design a composite process.
In summary, the CWL-M series centrifugal extraction technology shows good application prospects in the separation of toluene nitration products and neutralization and dephenolization. In the future, it can be further optimized in terms of equipment adaptive adjustment and intelligent control system to promote the widespread application of this technology in the field of fine chemicals.
Email: sales@tieiextraction.com
Whatsapp: +86 19069612820