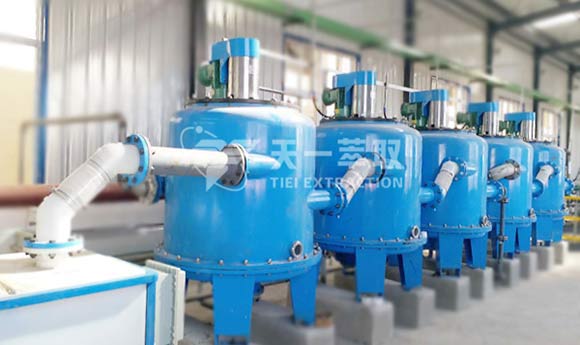
As global environmental regulations become increasingly stringent and the contradiction between nickel supply and demand intensifies, how to extract nickel from waste catalysts efficiently and environmentally friendly has become the focus of attention in the chemical, petrochemical, and new energy industries. As a new generation of efficient separation technology, centrifugal extractor is bringing disruptive changes to the field of nickel resource recycling with their process advantages of efficient separation and continuous operation.
Centrifugal Extractor for Nickel Recovery
The centrifugal extractor uses the strong centrifugal force generated by high-speed rotation to complete the mixing, mass transfer and phase separation of the extractant and the nickel-containing solution in milliseconds. Its core principles are:
Liquid liquid extraction: The selective complexing ability of the organic phase extractant on nickel ions is used to transfer nickel from the acidic leaching solution to the organic phase.
Multi-stage countercurrent enhancement: The nickel ions are enriched in stages through multi-stage series connection, and the separation efficiency is increased by 3-5 times compared with the traditional mixer settler.
Precise separation of two phases: The oil and water phases are quickly separated under the centrifugal field, and the phase separation time is shortened to 10-30 seconds to avoid emulsification and entrainment losses.
Process Flow of Nickel Recovery by Centrifugal Extractor
1.Raw Material Pretreatment
After the spent catalyst is crushed and acid-leached (H₂SO₄/HCl system), nickel enters the leaching solution in the form of Ni²⁺, and solid impurities are removed by filtration to obtain a nickel-containing solution with a pH of 2-3.
2.Centrifugal Extraction Enrichment
Extraction section: The nickel-containing solution and the organic phase (such as LIX84, Cyanex272 and other extractants) are in countercurrent contact in the centrifuge, and the nickel ions are selectively extracted into the organic phase.
Washing section: Remove co-extracted impurities (Fe³⁺, Al³⁺, etc.) to improve the purity of nickel.
Stripping section: Use dilute sulfuric acid to strip to obtain a high-concentration nickel sulfate solution (Ni≥50g/L).
3.Deep Purification
The stripping solution is treated by electrowinning or crystallization to produce electrowinning nickel plates (purity ≥ 99.9%) or battery-grade nickel sulfate crystals.
Why Choose the Centrifugal Extractor?
- Efficiency Revolution
The throughput of a single equipment can reach 5-50m³/h, and the processing speed is 10 times higher than that of traditional extraction column.
Nickel recovery rate>98%, organic phase loss<0.5%. - Cost optimization
The equipment footprint is reduced by 80%, and energy consumption is reduced by 40%.
The recycling rate of the extractant is over 95%, and the operating cost is saved by 30%. - Environmental upgrade
Closed-loop design reduces wastewater discharge by 90%.
No VOCs volatilization, in compliance with international environmental standards such as REACH and RoHS. - Intelligent control
PLC automatically adjusts the speed and flow ratio parameters to adapt to raw material fluctuations.
Online monitoring of nickel concentration to ensure product consistency.
Email: sales@tieiextraction.com
Whatsapp: +86 19069612820