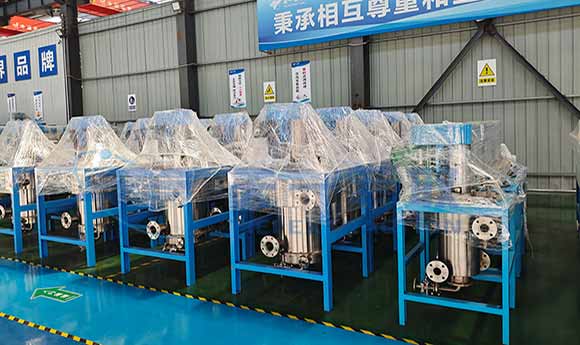
As an important chemical intermediate, the separation and purification process of nitrotoluene has long faced the dual challenges of efficiency and energy consumption. This study innovatively introduced centrifugal extraction technology to address the technical pain points of the traditional three-stage separator process, such as low separation efficiency, sodium phenol salt blockage, and high energy consumption, and achieved breakthrough progress through systematic process optimization.
The experiment used Zhengzhou Tiei Extraction CWL50-M centrifugal extractor, focusing on optimizing three key process links:
1.In the organic phase/acid phase separation stage, the oleic acid entrainment rate was reduced by precisely adjusting the weir plate size and controlling the feed flow rate;
2.In the alkali washing process, it was found that increasing the temperature to 50°C could completely inhibit the precipitation of sodium phenolate (no crystalline phase detected by XRD), and combined with a 2:1 alkali solution/organic phase ratio, the dephenolization efficiency was increased to 99.5%;
3.In the water washing stage, a coordinated strategy of temperature increase (60°C) and dynamic specific gravity adjustment was adopted, and the phase separation time was shortened by 60%, and the product purity was stabilized at more than 99.8%.
Compared with traditional processes, data show that the new process reduces energy consumption by 42%, increases production efficiency by 2.3 times, and reduces equipment footprint by 65%.
The innovative value of this study lies in: establishing a process parameter database for centrifugal extractors to treat nitrotoluene; developing a multivariable control model for temperature-flow-weir size; and proposing a gradual transformation plan of "local equipment replacement + process parameter optimization".
Industrial pilot tests have shown that this technology is particularly suitable for continuous production lines with an annual output of more than 10,000 tons. Under the premise of maintaining the original plant layout, capacity can be increased only by upgrading key equipment. For the flexible demand for multi-variety switching production, it is recommended to adopt a composite process design of "centrifugal extraction + traditional layer separator" to ensure separation efficiency and take into account operational flexibility. Subsequent research will focus on the development of intelligent control systems to further promote the application and expansion of this technology in the field of high value-added fine chemical separation.
The CWL-M series centrifugal extractor launched by Zhengzhou Tiei Extraction is developed to address the shortcomings of traditional centrifugal extractor. The power consumption is only 10% to 30% of that of traditional annular gap extractors. At the same time, the centrifugal extractor has short stage retention time, rapid phase separation, high extraction efficiency, and save investment costs and solvent recovery and regeneration costs.
Email: sales@tieiextraction.com
Whatsapp: +86 19069612820