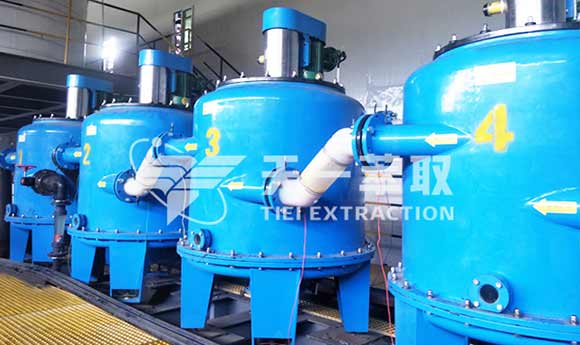
- Introduction
N, N-dimethylformamide (DMF) is an organic solvent widely used in chemical industry, medicine, pesticides, fiber and other fields. For example, it can be used for the extraction of aromatic hydrocarbons, the separation and recovery of butadiene from the C4 fraction, and the separation and recovery of isoprene from the C5 fraction. It can also be used as an effective reagent to separate non-hydrocarbon components from paraffin wax. In the pesticide industry, it can be used to produce insecticides. And in the pharmaceutical industry, it can be used to produce iodine, doxycycline, cortisone, etc., as well as in the production of acrylic, chlorine, etc. However, DMF produces a large amount of wastewater during the production process, especially in the chemical fiber wet spinning process. DMF coagulation bath or washing wastewater with low concentration can cause harm to the environment. Therefore, recycling and treating DMF wastewater is crucial.
- Traditional distillation process
The traditional distillation process can effectively recover DMF. This is due to the 53°C boiling point difference between n,n-dimethylformamide and water, and there is no azeotrope formation between them. Therefore, the effective recovery of n,n-dimethylformamide can be achieved simply by using the distillation process. However, this treatment method requires a large amount of water with high vaporization enthalpy to be evaporated from the top of the tower, so the process energy consumption is very huge, especially for low-concentration wastewater.
- Extraction-distillation process
This method replaces water with high vaporization enthalpy into other solvents through extraction, and then recovers refined DMF through distillation. The study found that using the CWL-M centrifugal extractor and using chloroform and/or dichloromethane as the extraction agent can separate most organic matter and DMF solvents from industrial wastewater containing high concentrations of organic matter, DMF and salts. This makes it relatively easy to separate the water from the mixed salt during the subsequent wastewater evaporation process to avoid foaming of the organic matter and the formation of a viscous paste from the organic matter and the mixed salt.
- Actual cases
Zhengzhou Tiei Extraction uses centrifugal extraction + distillation process in the recovery and treatment case of DMF wastewater discharged from a fine chemical factory. It was determined that the concentration of DMF in the original wastewater was 15%. The main extraction process flow is: dichloromethane is used as the extraction agent and enters from the light phase feed port of the centrifugal extractor. At the same time, DMF wastewater enters from the heavy phase feed port of the CWL-M centrifugal extractor. The ratio is set to 1:2. At a temperature of 25°C, the extraction phase is obtained through the light phase outlet of the CWL-M centrifugal extractor. Then, perform a distillation operation on the obtained extraction phase, and pass the obtained fractions through a dehydration column and a decolorization column for further purification, and finally obtain a high-purity DMF product. It has been determined that the purity of DMF in the product is 99.90% and the moisture content is 398ppm. The quality fully meets the requirements for recycling of spinning organic solvents.
If you want to know more about the wastewater DMF recovery and extraction process and equipment technology principles, please contact us and we will provide you with comprehensive technical services.
Email: sales@tieiextraction.com