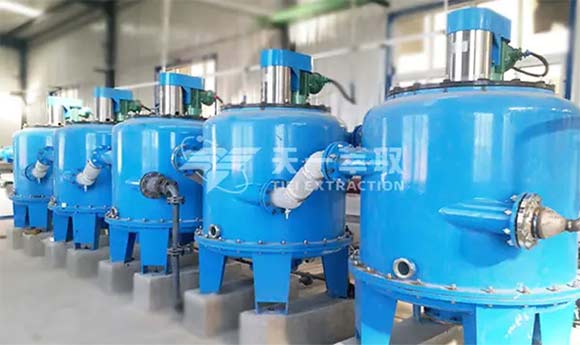
Against the backdrop of global resource shortages and increasing environmental pressure, platinum group metals (PGMs), as strategic key metal resources, have become a key focus of countries' competitive layout for efficient recovery and recycling. Platinum group metals include ruthenium, rhodium, palladium, osmium, iridium, platinum, etc., which are widely used in automobile exhaust purification catalysts, petrochemical catalysts, fuel cells, electronic devices and other fields, and have irreplaceable technical and economic value.
In the PGMs recovery process, the low-temperature iron capture-electrolysis-centrifugal extraction process is gradually replacing the traditional chemical precipitation method and other old processes with long processes and high material consumption due to its advantages of efficient mass transfer, rapid phase separation and strong selectivity. It has become one of the core technologies in wet recovery and is pushing the separation and purification of PGMs to a new stage of short process, low cost and high purity.
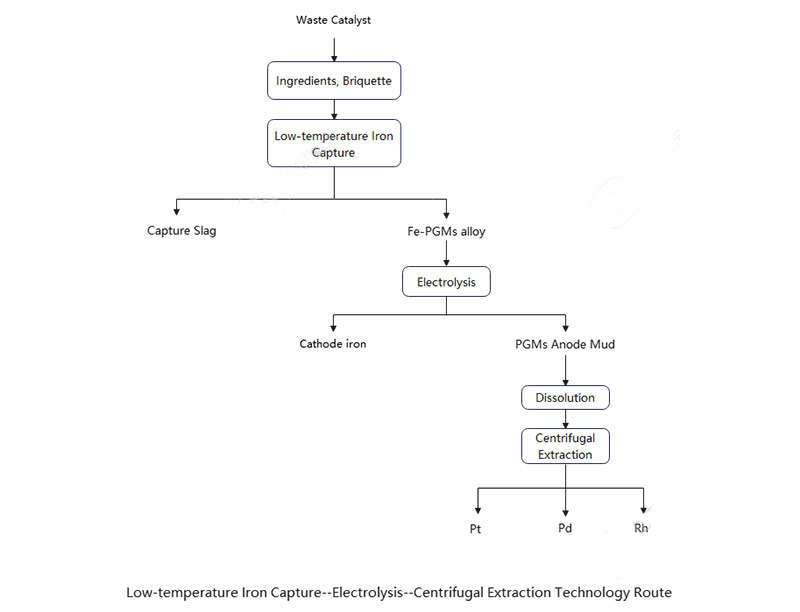
Centrifugal Extraction Technology Enables Efficient Recovery of PGMs
In recent years, with the development of the integrated process of "low-temperature iron capture--electrolysis--centrifugal extraction", PGMs recovery has achieved full process from pyrometallurgical enrichment to hydrometallurgical purification. This process uses iron-based alloys as collectors to selectively capture PGMs under low temperature conditions, and further enrich PGMs into anode mud through constant pressure electrolysis. Subsequently, centrifugal extraction technology is used to achieve efficient separation of palladium, platinum, and rhodium in turn:
- Diisoamyl sulfide (S21): can efficiently extract palladium ions and achieve effective separation of palladium from other metals;
- Tributyl phosphate (TBP): used for selective extraction of platinum, entering the organic phase through the complex cation formed with H+;
- Rhodium is retained in the aqueous phase because it cannot be effectively extracted by the above extractants, thus achieving the separation of the three.
After stripping and reduction treatment, palladium, platinum and rhodium products with a purity of more than 99.95% are finally obtained, truly realizing the efficient recovery and high-value utilization of PGMs.
Advantages of Centrifugal Extraction Technology
- Efficient mass transfer: The shear force generated by high-speed rotation allows the two phases to fully contact, greatly improving the mass transfer efficiency.
- Rapid phase separation: Under the action of centrifugal force, the organic phase and the aqueous phase are quickly separated, shortening the operation time.
- Strong adaptability: It can flexibly cope with material systems of different densities and viscosities by replacing the weir plate and adjusting the speed.
- Green and environmentally friendly: Reduce the use of toxic reagents and reduce wastewater discharge, in line with the concept of green manufacturing.
- High degree of automation: Support continuous feeding and discharging, facilitating system integration and intelligent control.
At present, this technology has been successfully applied in many PGMs recycling companies, and is particularly suitable for the treatment of complex raw material systems containing waste catalysts, waste electronic components, waste jewelry, etc.
Email: sales@tieiextraction.com
Whatsapp: +86 19069612820