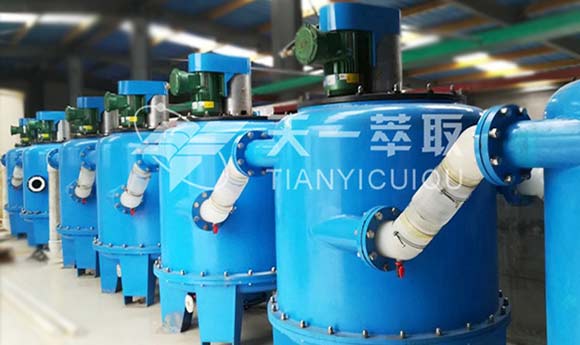
As an important strategic metal, vanadium is widely used in aerospace, medicine, all-vanadium flow battery energy storage, etc. Among them, vanadium shale is a low-grade polymetallic ore with abundant reserves. At present, the vanadium-containing leaching solution obtained from the vanadium shale extraction process mainly uses solvent extraction and ion exchange to separate and enrich vanadium and impurities.
Vanadium shale acid leaching solution contains a variety of impurity elements, especially the presence of iron, which makes the purification of vanadium extremely difficult. Traditional solvent extraction methods usually require multiple stages in series to achieve effective separation, which not only increases equipment investment and operating costs, but also leads to the problem that separation purity and efficiency are difficult to achieve at the same time. How to efficiently separate high-purity vanadium from vanadium shale acid leaching solution has become a key issue that the industry needs to solve urgently.
At present, solvent extraction is widely used in the industrial production of vanadium extraction from vanadium shale due to its advantages such as strong stability, high enrichment ratio and convenient operation. The commonly used extractant is di(2-ethylhexyl) phosphate (P204), which can effectively enrich vanadium and separate it from its impurities. However, P204 has poor selectivity for Fe(III) and V. Therefore, in order to avoid the co-extraction of Fe(III), it is usually necessary to add excess reducing agent to reduce Fe(III) to Fe(II), thereby reducing the extraction rate of Fe. The working principle of centrifugal extraction technology is to accelerate the forced mixing and rapid separation of two-phase liquids through the centrifugal force generated by high-speed rotation, overcoming many disadvantages of traditional methods. Taking the acid leaching solution of a vanadium shale as an example, the typical process flow of separating vanadium iron using centrifugal extraction technology is as follows:
- Countercurrent extraction: The vanadium-containing acid leaching solution is countercurrently contacted with the extractant (such as P204), and the vanadium is preferentially complexed with the extractant and enters the organic phase, while the iron is enriched in the aqueous phase.
- Washing and purification: The organic phase loaded with vanadium is washed with dilute acid to remove the trace impurities carried by it and further improve the purity of vanadium.
- Stripping: The vanadium in the organic phase is stripped with an acidic solution to obtain a high-purity vanadium-enriched solution.
Studies have shown that in the centrifugal extraction process, when the volume ratio of P204 increases from 15% to 40%, the vanadium extraction rate increases from 87% to 93.84%. At the same time, under the same conditions, the vanadium extraction rate obtained by the conventional extraction process is always lower than the vanadium extraction rate in the centrifugal extraction process. In addition, the vanadium extraction capacity in the centrifugal extraction process can reach 70.45 g/L, while it is only 52.63 g/L in the conventional extraction process. The Fe extraction rate in the centrifugal extraction process is reduced from 11.9% to 5.3%, and the V/Fe separation coefficient is increased from 41.78 to 127.
Advantages of CWL-M Centrifugal Extractor
- Low power consumption: The energy-saving effect is obvious. Under the same processing capacity, the power consumption is only 1/3-1/10 of that of traditional extraction equipment.
- No vulnerable parts: The centrifugal extractor adopts an upper suspension structure, which cancels the bottom mechanical seal of the traditional model, thus completely solving the problem of bottom leakage and easy damage of the mechanical seal of the traditional model.
- Simple and stable structure: The centrifugal extractor has simplified the body from the beginning of design, making the operation simpler and the operation more stable.
- Weir plate replacement: The centrifugal extractor can realize the rapid replacement of the heavy phase weir plate.
The application of centrifugal extractors in separating vanadium iron from vanadium shale acid leaching solution not only achieves efficient separation of vanadium elements, but also promotes the development of the vanadium industry in a green and efficient direction. Through efficient mass transfer processes, rapid separation capabilities and intelligent control methods, centrifugal extraction technology has greatly improved the recovery rate of vanadium and product quality, and reduced production costs and environmental impact.
Email: sales@tieiextraction.com
Whatsapp: +86 19069612820