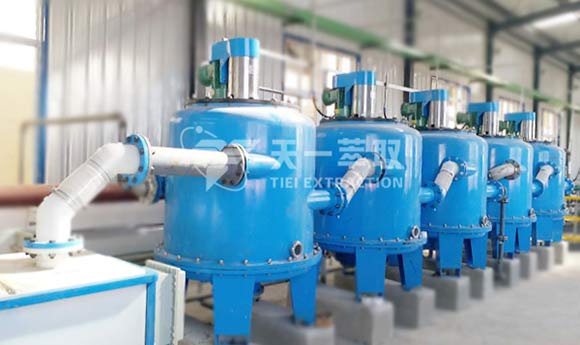
With the rapid development of the new energy vehicle industry, the demand for lithium-ion batteries is increasing year by year. Lithium iron phosphate batteriy is widely used in the new energy vehicle and energy storage markets due to their high energy density, good safety, and long cycle life. However, the energy density, output power and other indicators of lithium-ion batteries have been continuously optimized. At the same time, with the surge in the number of electric vehicles and the accelerated development of energy storage equipment, the demand for lithium-ion batteries has increased year by year, and lithium resources have gradually become in short supply. Therefore, the recycling of used lithium-ion batteries is particularly important.
The current method of recycling waste lithium iron phosphate battery materials can separate and recover different elements in the lithium iron phosphate materials, but the purity of the recycled products varies. Introducing a method with high recovery rate and high purity of recovered products. The electrochemical performance of lithium iron phosphate batteries prepared from the products recovered by this method cannot meet the requirements. The specific process includes:
- Pretreatment: First, the positive electrode active powder recovered from used lithium iron phosphate batteries is matured.
- Leaching: Adopt two-stage countercurrent leaching process is used to leach the matured materials to obtain a leachate containing phosphate ions, ferrous ions and lithium ions.
- Extraction and impurity removal: Add iron powder to the leachate, filter to remove copper powder, and then continue to add aluminum extraction agent (such as a mixture of bis(2-ethylhexyl)phosphate and sulfonated kerosene) to the leachate. This extraction section uses a CWL-M centrifugal extractor, in which the volume ratio of aluminum extraction agent and leachate entering the centrifugal extractor is 1:1. The aqueous phase after extraction is the impurity-removing leachate. The CWL-M series centrifugal extractor is a new and efficient extraction equipment that can significantly reduce the amount of extraction agent, reduce the floor space, and reduce resource loss. The entire process is simple, low-cost, and has a high lithium recovery rate.
- Preparation of iron phosphate and lithium carbonate: By adding phosphoric acid and oxidizing agent, ferrous ions are oxidized into ferric ions, and the pH value of the system and the ratio of iron and phosphorus are controlled to obtain higher purity iron phosphate;Adding soluble carbonate can precipitate lithium ions and obtain higher purity lithium carbonate.
The iron phosphate and lithium carbonate prepared by the above recycling method have high purity, meet battery grade standards, and can be recycled as raw materials for preparing lithium iron phosphate cathode active materials.
This method has the advantages of high recovery rate and high purity. It can effectively recover valuable metals in used lithium iron phosphate batteries, realize resource recycling, and reduce environmental pollution at the same time.
Email: sales@tieiextraction.com