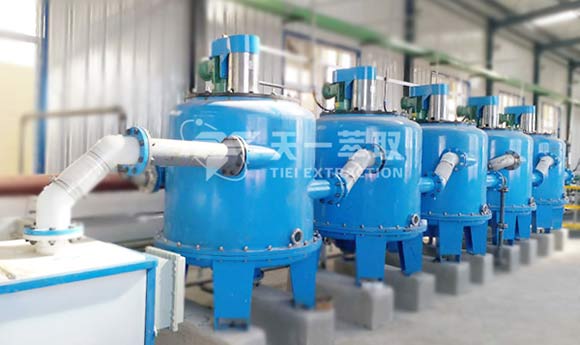
In the process of tin smelting and recovery, how to efficiently and selectively separate and enrich tin from complex leaching solutions (such as cassiterite sulfuric acid leaching solutions and electronic waste recycling solutions) is the key to improving resource utilization and economic benefits. Solvent extraction technology has become one of the core technologies of modern tin hydrometallurgy with its advantages of high selectivity, high enrichment ratio and easy continuous operation.
Tin Solvent Extraction Process (taking acid leaching solution as an example)
1.Raw material preparation: Tin-containing acidic leaching solution (aqueous phase) usually needs to be pretreated, such as filtering to remove suspended solids and adjusting the appropriate acidity and tin concentration.
2.Extraction agent selection and preparation:
Commonly used extractants: Phosphoric acid extractants (such as di(2-ethylhexyl)phosphoric acid, D2EHPA), phosphonic acid extractants (such as 2-ethylhexylphosphonic acid mono-2-ethylhexyl ester, PC-88A), hydroxyoxime extractants (such as LIX series) have good selectivity and extraction capacity for tin (IV).
Organic phase preparation: The selected extractant is dissolved in a suitable diluent (such as kerosene, sulfonated kerosene) to form an organic phase. Modifiers (such as TBP, isodecyl alcohol) are usually added to prevent the formation of the third phase and improve the phase separation performance.
3.Extraction stage (centrifugal extractor):
The tin-containing acidic leaching solution (aqueous phase) and the prepared organic phase continuously enter the centrifugal extractor in a certain ratio (flow ratio).
Inside the centrifugal extractor, the two phases are quickly mixed and sheared under the action of a strong centrifugal field, achieving efficient mass transfer of tin ions from the aqueous phase to the organic phase.
The mixed two phases are quickly separated under the action of centrifugal force. The organic phase loaded with tin (loaded organic phase) has a lower density and is discharged from the light phase outlet of the centrifugal extractor; the raffinate (aqueous phase after tin extraction, containing impurities) has a higher density and is discharged from the heavy phase outlet.
A multi-stage countercurrent extraction process is usually used to maximize the recovery rate of tin.
4.Washing stage (centrifugal extractor):
The loaded organic phase may carry a small amount of impurity ions or acids.
Washing with dilute acid solution or water in a centrifugal extractor removes these impurities and improves the purity of the tin product. The washing liquid is returned to the extraction section or treated separately.
5.Stripping stage (centrifugal extractor):
Use a suitable stripping agent (usually a strong alkaline solution) to contact the loaded organic phase in a centrifugal extractor.
Under the centrifugal field, the tin ions are stripped from the organic phase into the alkaline solution to form a sodium stannate (Na₂SnO₃ or Na₂Sn(OH)₆) solution (stripping solution).
The regenerated organic phase (lean organic phase) is recycled back to the extraction section for reuse.
Multi-stage countercurrent stripping is also used to improve the stripping efficiency.
6.Tin product recycling:
The tin-rich stripping solution (sodium stannate solution) can be obtained by:
Electrolytic deposition: Direct electrolysis to obtain high-purity metallic tin.
Hydrolytic precipitation: Adjust the conditions to precipitate stannic acid, and then calcine to obtain tin dioxide (SnO₂).
Crystallization: Obtain sodium stannate crystals.
Advantages of Solvent Extraction for Separating Tin
1.High selectivity: The selected extractant can preferentially extract tin (IV) and effectively separate the impurity ions such as iron, arsenic, antimony, copper, zinc, etc. coexisting in the leachate.
2.High enrichment ratio: It can concentrate the low-concentration tin leachate into a high-concentration tin solution (stripping solution), significantly reducing the scale and cost of subsequent processing.
3.High recovery rate: Through multi-stage countercurrent operation, the recovery rate of tin can usually reach more than 95% or even higher.
4.High product purity: Through extraction and washing, impurities can be effectively removed to obtain tin products or intermediates (such as sodium stannate) with purity that meets market requirements.
5.Continuous and automated operation: It is easy to achieve continuous and automated control of the production process, improve production efficiency, stabilize product quality, and reduce labor costs.
6.Reagents can be recycled: The organic phase (extractant and diluent) is recycled in a closed-loop system, with low consumption and relatively controllable operating costs.
Centrifugal Extractor Advantages
In the solvent extraction process of tin, centrifugal extractor has incomparable advantages over traditional mixer settler or extraction column:
1.Strong centrifugal separation: Using the centrifugal force of hundreds to thousands of times gravity, the two-phase separation is completed instantly (usually only a few seconds to tens of seconds), completely solving the emulsification problem and having a large processing capacity.
2.Short stage residence time: The material stays in a single equipment for a very short time (usually 1-3 minutes), reducing the risk of solvent degradation and side reactions, and is particularly suitable for processing unstable systems.
3.Processing systems with small density difference between two phases/easy to emulsify: The strong centrifugal force enables it to process systems with similar density or easy to emulsify that are difficult to separate with traditional equipment.
4.Closed operation: Fully enclosed structure effectively reduces the escape of volatile organic solvents (VOCs), improves the working environment and ensures safety.
5.High degree of automation: Easy to integrate with DCS/PLC system to achieve precise flow and speed control, easy operation and labor saving.
6.Operation cost advantage: High separation efficiency, reduced solvent entrainment loss; short residence time, reduced solvent degradation; compact equipment, reduced energy consumption and maintenance costs.
Centrifugal extractor has become the preferred equipment for modern tin solvent extraction plants due to their core advantages such as ultra-fast separation, high mass transfer efficiency, airtight safety, and significant savings in land/investment. They bring into full play the inherent advantages of tin solvent extraction technology such as high selectivity, high recovery rate, and high product purity. They not only greatly improve the process level and economic benefits of tin smelting and recycling, but also meet the requirements of modern industry for green, efficient, and intelligent production. The application of centrifugal extraction technology undoubtedly marks a new era of more efficient and reliable tin separation and extraction technology.
Email: sales@tieiextraction.com
Whatsapp: +86 19069612820